Wipotec Weigh Cells have always used the principle of force restoration in combination with a monolithic aluminum block – the Wipotec monoblock. Up to now, this has been produced on a CNC-controlled cutting machine. A monoblock weighing around five kilograms forms the core of a high-precision, industrialgrade automatic scale, which can dynamically weigh 15 kilograms of load capacity with maximum accuracy at high transport speeds.
In the pharmaceutical sector, there are different requirements: here it is a question of milligrams or micrograms. The monoblocks used are delicate and weigh just a few grams. But they are also produced fully automatically on ultra-precise tool machines, the acquisition costs of which can be in the seven-figure range.
Wipotec
“3D printing is a quantum leap in the design of monoblocks.”
— Bernd Zinke, Head of Metrology
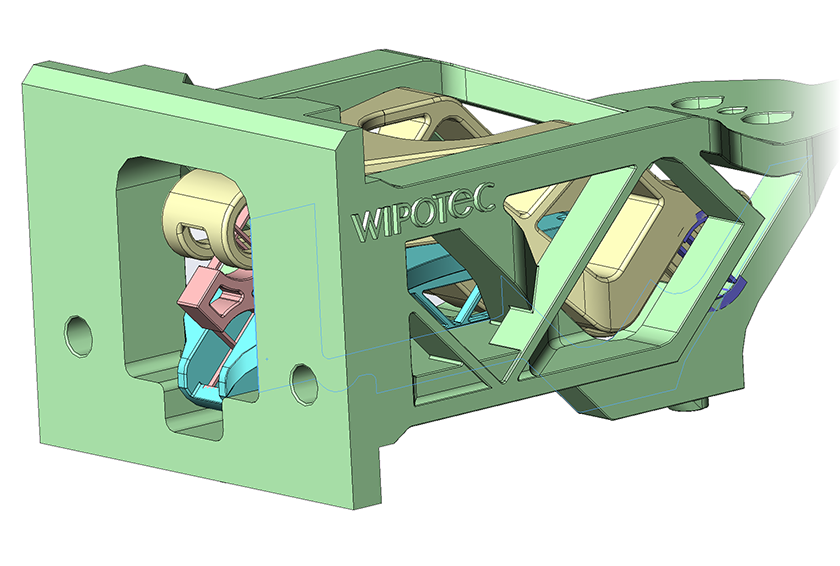
It all started in 2D
Initially, the geometry of the controller and lever mechanism of the finished monoblocks was only two-dimensional, until the ability to create undercuts was added with the advances in 3D machining technology, which then made it possible to create more complex and smaller structures.
However, this technology is now also reaching its own limitations – specifically when different components of the monoblock’s controller and lever mechanism need to be arranged in an even more space-saving arrangement, nested inside each other. This is precisely where 3D printing comes in.
A technology on the move
Several years ago, Wipotec began to conceive and design monoblocks that were suitable for 3D printing technology. In 3D printing, one material layer is applied after the other and is liquefied by a laser beam so that it can bond with the previous layer (additive manufacturing).
Completely new design possibilities arise in particular from the fact that the layered material structure of one monoblock component can be interrupted by the material structure of another component. Wipotec has now filed several patent applications for 3D printing technology in weighing technology, in which various materials are also used for different structures.
What will be possible in the future
Monoblocks produced using 3D printing look very different than previous monoblocks. Their size has “shrunk” and they comprise much less material, which is positive for the ecological balance. The test methods also need to be redesigned, as the highly nested structure means that tactile measurement methods can no longer reach all the required measurement locations. X-ray processes are thus in demand, a technology that Wipotec also develops and manufactures in-house
A technological quantum leap
3D printing technology is now widely used in various industries, for example for printing lightweight frameworks and in lightweight construction. It is also used in prototype construction, for example in some areas of automotive engineering. However, in weighing technology it is still in its infancy, and Wipotec is definitely a pioneer with regard to new design possibilities for monoblock geometries. In future, the aim will be to use this technology more cost effectively in series production.
The future of monoblocks at Wipotec may no longer be in machining, but it will be all the more exciting...